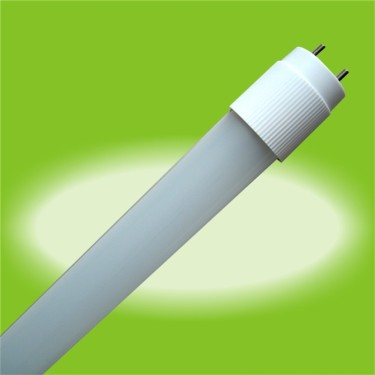
The shortage of LED high-end talent in the mainland is the most important manifestation of the relative lag in the overall development of the mainland LED industry. Now that the LED patent warfare has started, the lack of core technical personnel has become a bottleneck for the development of various enterprises. If LED companies want to have a good development, they must solve the problem of shortage of talent.
Talent issues constrain the development of the industry At present, LED people generally believe that the future of the LED industry will be the trend of survival of the fittest. It is very important for companies to develop, improve their core competitiveness and train their talents. In the past few years, LED industry has made great strides, the industry has not established a mature talent training mechanism, lacks fresh blood input, and lacks of sustainable development.
The upstream of the industrial chain such as epitaxial chips is the most scarce. Taking the MOCVD equipment as an example, the American VEECO and the German AIXTRON companies account for 90% to 95% of the global market share. Although Japanese equipment is also more advanced, it is basically self-owned and rarely exported. Many mainland companies do not understand the actual situation and think that with the equipment, they can directly go into production. After spending heavily on equipment purchased in the United States and Germany, it was discovered that there was a lack of knowledgeable and truly experienced personnel to debug and operate the equipment. These enterprises have had to dig people from Taiwan, South Korea and other places with high salaries in order to understand the urgency. This is not uncommon.
At present, most of the core technologies of the LED industry are in the hands of Japan and the United States. On the one hand, the mainland's investment in new technologies and new products is not as large as in developed countries. Enterprises want to maximize their profits in the short term. On the other hand, China's LED industry is indeed developing too fast and natural professionals are in short supply.
China's high-efficiency, high-reliability LED raw materials are almost all dependent on imports. The core technology of high-grade epitaxial chip production processes is controlled by people, especially the upstream chip patent technologies are mostly controlled by foreign large manufacturers. With the rise of LED patent war smoke, mainland companies are more aware of the importance of talent. However, incompatible with the rapid development of the LED industry, the current professional setting of counterparts in mainland universities and colleges has only just begun, and LED talents cannot yet be transported in batches by related institutions. If the talent shortage problem cannot be solved, the development of the LED industry will undoubtedly be constrained.
The lack of a true backbone of the company's business as a key driver is almost the most troublesome thing for all the bosses. Bringing talented people together, both before and now, is what leaders should do. How many people have the ability to think of companies is an important factor that affects the success or failure of the company. This led to a dig in the LED industry...
In recent years, many companies with capital backing and just getting involved in the LED industry are eager to quickly establish an “airdrop†elite team that can make immediate achievements. In order to solve the urgency, hiring high-level talent from Taiwan has become the first choice for many mainland companies.
Since the end of 2010, mainland manufacturers have frequently used high-paying talents to reduce Taiwan’s talents to reduce learning curve time. For example, Sanan Optoelectronics is frequently chasing talents in the crystal industry.
For the majority of enterprises, it is understandable to seek talents through enthralling the introduction of talents. The so-called “trees are dead, people are movedâ€, but we must look to the long-term, overcome the mentality of quick success and instant benefit, if there is no innovative soil and environment, even from the outside It is very difficult to survive when people are dug up, and it will gradually wither.
Long-term vision to cultivate innovative talents It is understood that in recent years, Japan, South Korea, Europe and the United States and other countries have used special funds to fund LED professional technical training in order to support the development of their LED industry, providing a source for the development of the industry. Constant reserve forces. At present, China's specific plans in this area have not yet been introduced, and companies have begun to explore the path of talent cultivation.
Chinese LED enterprises should combine short and long term goals in personnel issues, the introduction of independent training combined. In addition, industry associations and institutions such as the majority of associations and societies should also start with special training, technical exchanges, and other activities, and actively participate in the construction of a talent cultivation system. Training talent requires investment and it takes more time. Looking into the future for some time, the status of China's LED talent will certainly improve, but to what extent it can be improved, it also requires everyone to work together.
Looking forward to 2013, due to the localization of many technologies including MOCVD, sapphire equipment, and GaN substrates in the upper reaches of LED, it will accelerate the localization process of the entire LED industry. At the same time, as the LED industry in the Chinese mainland lacks LED high-end talents, it will cultivate talents. It is also not a business day, so in 2013 China's LED industry will still face the pain of lack of talent.
Plated Plastic Housing Coffee Grinder
Coffee Mill Grinder,Coffee Grinder Machine,Automatic Coffee Grinder,Plated Plastic Housing Coffee Grinder
FOSHAN FORTUNE ELECTRICAL APPLIANCE CO.,LTD , https://www.coffelady.com